
Create and/or organize a production schedule on a daily basis and also make sure that every output (level) is recorded appropriately in the correct system.
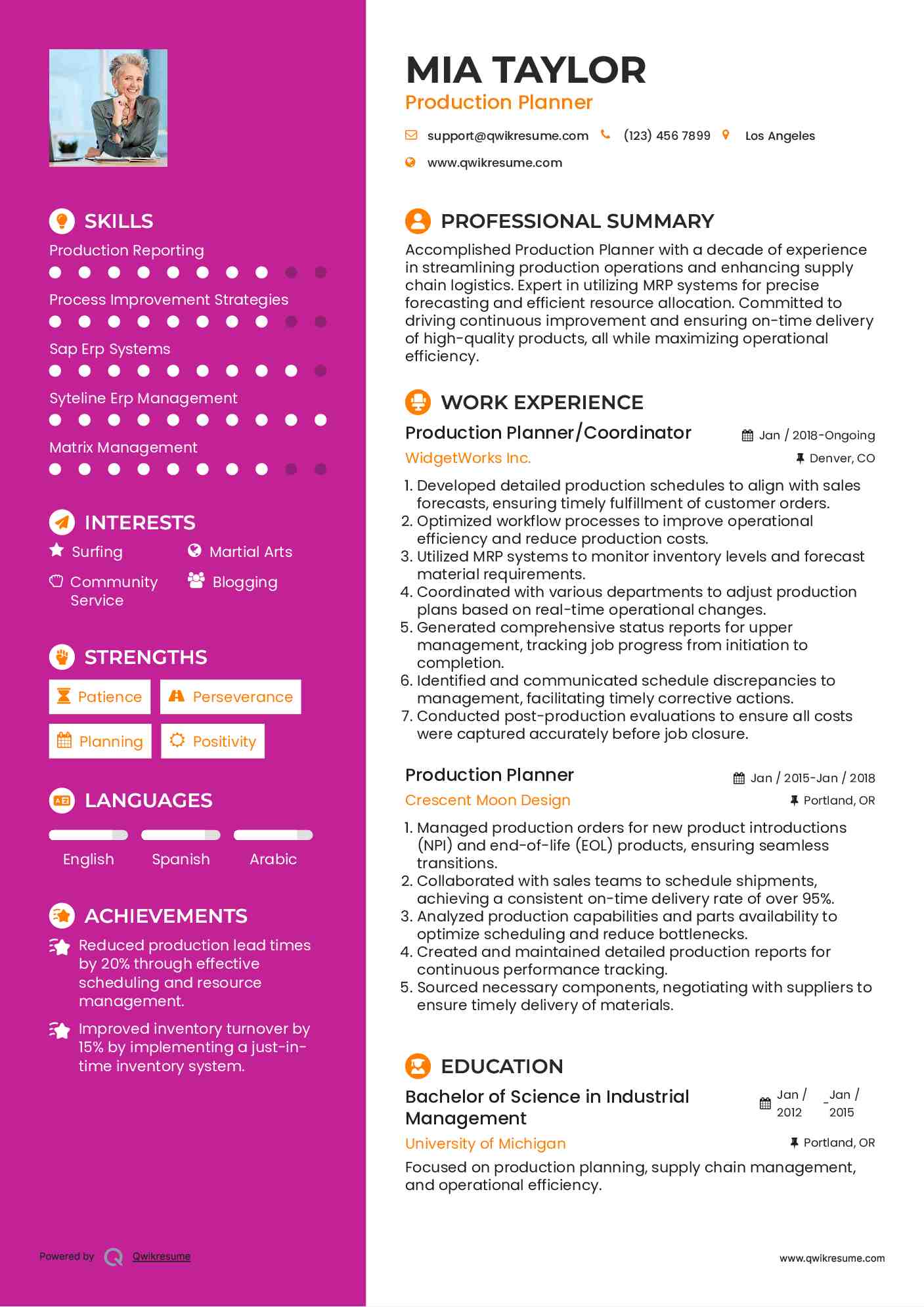
The job description below is a typical example of the kind of tasks, duties, and responsibilities commonly assigned to persons who work as master schedulers in most organizations: Master Scheduler Job Description Example/TemplateĪ master scheduler performs various functions in ensuring that work being done within a company is performed in a particular order so as to attain efficiency, and to also make sure that whatever product being rendered by a company meets or surpasses a particular standard and/or required level. The master scheduler job description entails ensuring that all the different processes and schedules being set by an organization are followed judiciously so as to attain great efficiency.Ī master scheduler usually works for a large firm that operates in the manufacturing sector, but can also work in certain places like other (large) private and government facilities, and hospitals. Master Scheduler Job Description, Duties, and ResponsibilitiesĪ master scheduler is responsible for coordinating, planning, scheduling, and supervising products throughout their production process or cycle. We celebrate diversity and Gibson Brands, Inc is an Equal Opportunity employer.Aluminium production: Master schedulers ensure smooth manufacturing process. We operate in a fast-moving and competitive global environment and therefore need employees to be flexible. The company’s Job Descriptions are not intended to be a complete detailed account of all expected/anticipated activities. Relish working in a company with a diverse, challenging, and fast paced environment.Able to proactively question and challenge to prioritize and identify solutions in timely manner
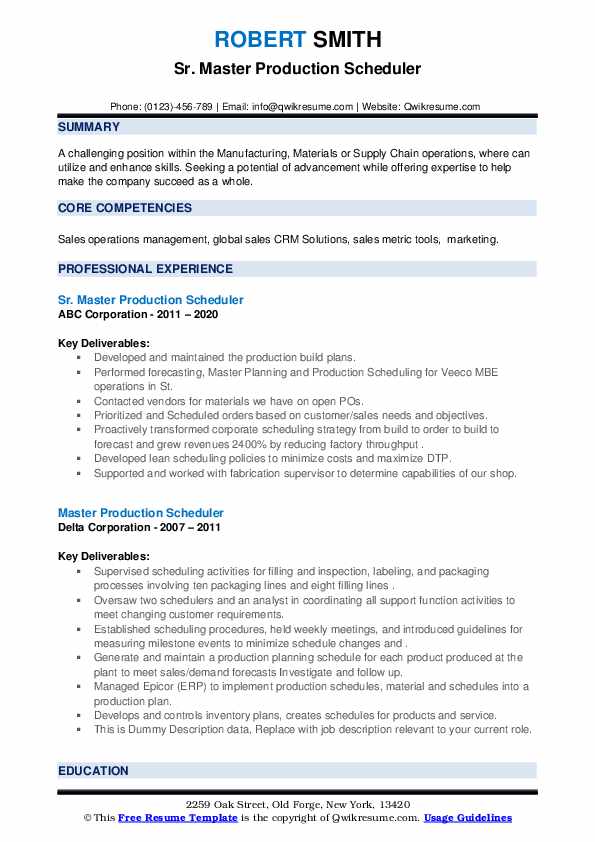
Flexibility to adapt quickly to changing circumstances.Results oriented and driven, with a track record for delivering to plan.Passionate about working and winning in a team environment.Project management skills combined with ability to work as part of a team.Outstanding time management skillset with the ability to prioritize without direct supervision.Solutions oriented approach to challenges/issues (Problem Solving discipline).Familiarity with a manufacturing environment.Excellent written and oral communication skills.Knowledge of, and prior experience in Lean concepts in operations planning.Preferred minimum experience of 5 years in a high mix, low volume production environment in a relatable role.Experience working with physical inventories.Experience analyzing BOM consumption and discrepancies.Proficiency in MS word, excel and power point.Familiarity with ERP systems (Microsoft Dynamics or D365 preferable) in a production environment.Participates in formal process improvement events.Coordinates with master scheduler to review daily schedule performance related to high risk items.Generates report-outs related to findings and adjustments of inventory.Ability to read specification sheets and interpret impacts to bill of material development.Responsible for coordinating item setup, including bill of material review and development.Reviewing and responding to needed adjustments, delivering root cause analysis corrective actions.Communicates production plans and needs to company performance stakeholders.
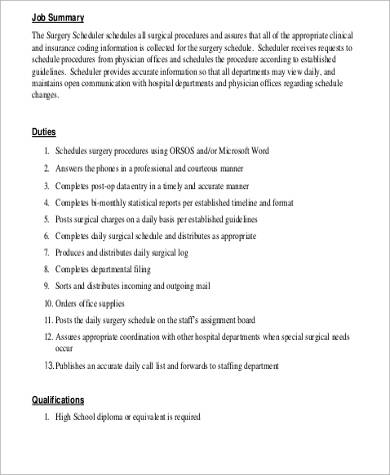
